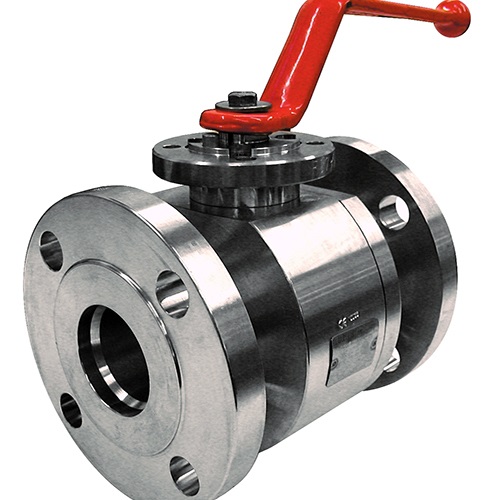
Features and Benefits
Increases durability as robust design with chemical coating and high performance cladding ensures continuous functioning even during severe service conditions and extreme environments.
Seat design to FCI 70-2 Class VI to perform on highest demands zero tightness
Reduces replacement cost as the performance capabilities of the valves can be easily upgraded and various chemical coatings can be applied to stem/seat arrangements to suit different applications
Improves plant safety as the valves are designed to meet fugitive emission standard ISO 15848
Configurations
Extreme High Cycle
Stem supported in bearings ensures seals are free from operation loads. Special bearing configurations including cladding of critical areas and trim coating configurations improve valve life-time.
Extreme High Temperature
Designed for temperatures up to +1022°F for the highest demands on valve tightness in process and to atmosphere (FE).
Solid Transport
Chambered ball seats, seat pocket body design, stem seal protection and flushing system designs support valve performance and extend service life-time.
Severe Service
Process optimized coatings, cladding option and wearing protectection feature extends ball valve life-time.
Flushing Systems
Flushing options in critical valve areas (e.g. on seats, stem or cavity) avoid media build up to improve service life-time.
Oxygen Service
High performance designs for high pressure, metal to metal seat gas tightness solutions in Oxygen service. In house Clean-room assembly and testing.
Special Alloys
Process and application related special alloys (e.g. Inconel, Monel, Alloy20, Titanium).
Special applications
Product Discharge valves, valve internal cladding for critical areas in abrasive and erosive environment, and ESD (Emerging Shut Down valves) units.